機械設計をしていると、「安全って大事だよね」という話をよく耳にします。でも実際に「安全にする」って、具体的には何をすればいいのでしょうか?
この記事では、機械設計を始めたばかりの方や、これから学ぼうとしている方に向けて、安全設計についての基礎的な考え方を解説します。
また、実際に安全設計を設計プロセスへの組み込む「リスクアセスメント」の手順についても触れていきます。初心者が知っておくべき基礎知識をまとめていますので、ぜひチェックしてみてください。
「安全である」とはどうゆうこと?
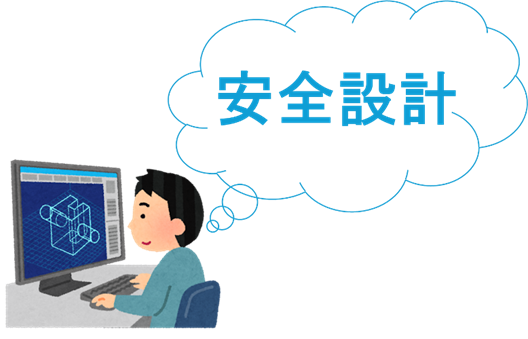
最初に、「安全である」とは何を指すのかをはっきりさせましょう。「安全」とは「受容できないリスクがない状態」と定義されています。つまり「ある程度のリスクは残っている」ということです。
たとえば、自動車を運転するときのリスクを考えてみましょう。
どんなに注意したとしても、事故が起きないとは言い切れません。しかし、エアバッグなどの装備があったり、交通ルールや信号があったりすることで事故が起きた際の「危害のひどさ」と「事故が起きる確率」はぐっと下がっています。つまり、「ある程度のリスクはあるけれど、なんとか受容できる範囲に収まっている」という状態です。「危ないところを全部なくそう!」と考えがちですが、実際には不可能なケースが多いですし、効率やコストの面で問題が出たりします。
安全設計のポイントは、「大きなリスクを見落とさないこと」と「リスクが起きても被害を最小限に抑えられるように工夫すること」。この考え方を押さえておくだけでも、日頃の設計作業がだいぶ変わってくるはずです。
リスクはゼロにならない

リスクは、「危害のひどさ × 危害の発生確率」で表されます。
- たとえば、機械に巻き込まれると大怪我をする――これは「危害のひどさ」が高いということ。
- 一方で、それが起きる確率が0.0001%――これは「発生確率」が低いということ。
初心者の方だと「どれだけひどい怪我や損害があるか」という「危害のひどさ」に目が行きがちですが、確率を無視してしまうと正しいリスク評価ができません。極端に言えば、危害がひどくでも、発生確率が極めて低ければ、リスクは低いと判断されます。逆に、傷は浅いが毎日のように誰かが怪我をするのであれば、そのリスクは見過ごせません。
つまり、設計時には「ひどさ」と「確率」両方をちゃんと見て、どれぐらい危険なのか、どんな対策が必要かを考える必要があるわけです。リスクを完璧にゼロにすることは不可能です。それを踏まえたうえで「このリスクはどうやって抑えるのか?」「残ったリスクは受容できるレベルなのか?」を考えることが、安全設計の第一歩です。
3つの安全設計手法
ここでは、3つの安全設計手法「フェールセーフ」「フォールトトレランス」「フールプルーフ」をご紹介します。リスクをゼロにできないからこそ、どんなふうにリスクを減らしていくのかを具体的にイメージしやすくなるはずです。
① 危害のひどさを下げる「フェールセーフ」
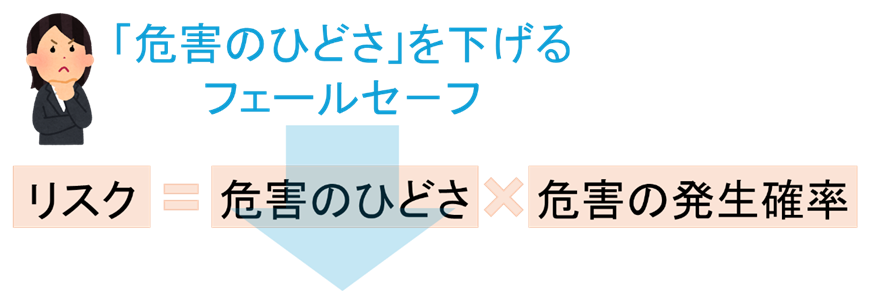
フェールセーフは「装置やシステムでなにか異常や故障が起こったとき、できるだけ安全な状態になるようにする」手法です。
- 例1: エレベーターのブレーキ
- 電源が切れたら自動的にブレーキがかかる仕組みになっているので、万が一停電が起きてもいきなり落下しません。
- 例2: 切断機の非常停止スイッチ
- スイッチ回路が断線したりボタンが壊れたりした場合、自動的に動作が停止する設計にしておくことで、危害を最小限に抑えます。
このように「何かがおかしくなったら、安全方向に動く(または停止する)」というのがフェールセーフの基本です。機械設計では、部品が壊れたり、センサーが誤動作したりしても、そこから大きな事故に繋がらないように考える必要があります。
② 危害のひどさを下げる「フォールトトレランス」
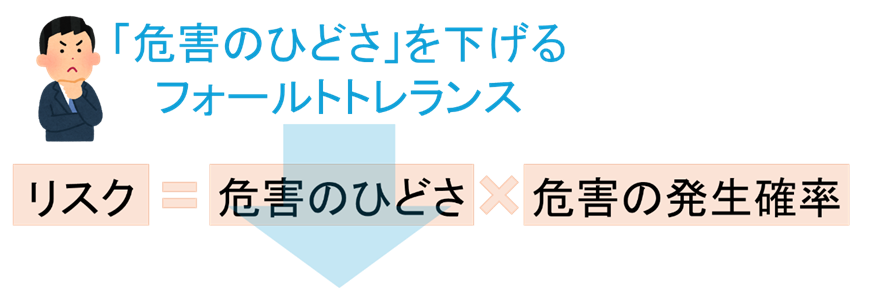
フォールトトレランスは、ある部分が故障しても、全体としては機能を維持できるようにする考え方です。フェールセーフと同じく「危害のひどさを減らす」アプローチではありますが、やり方が異なります。
- 例1: 飛行機のエンジンが複数搭載されている
- もし片方のエンジンが故障しても、もう一方で最低限の飛行を続けられるので、安全に着陸できる可能性が高まります。
- 例2: 冗長化された制御系統
- 制御システムが2重、3重になっている装置は、1つ壊れても別の系統がバックアップとして動作し続けます。
要するに「一部がダメになっても、全体はなるべく止まらないようにする」というのがフォールトトレランス。止まると危険や損害がさらに大きくなる装置(医療機器やプラント設備など)でよく使われます。ただし、冗長化するほど部品コストがかさんだり、仕組みが複雑になったりするので、どこまでやるかのバランスを取るのも重要です。
③ 危害の発生確率を下げる「フールプルーフ」
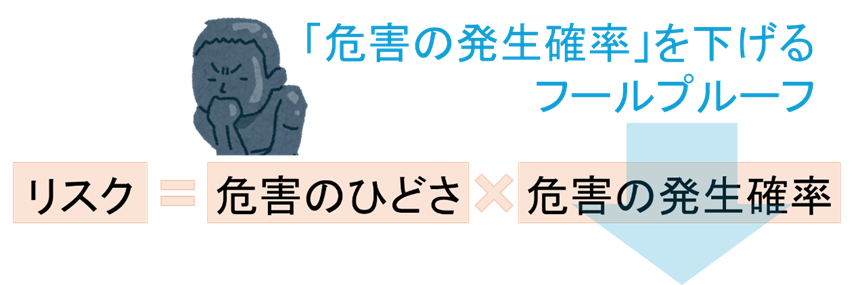
フールプルーフは、「誤操作ができないようにして、危険を減らす」ことです。人間はどうしてもミスや勘違いをしてしまうものですが、装置側がそうしたミスを物理的に防いでくれれば、リスクが発生する確率を下げられます。
- 例1: USB端子
- 裏表が合っていないと刺さらない形状になっているので、誤挿入を防いでいます。
- 例2: 自動車のAT(オートマチック)車のシフトロック
- ブレーキを踏んでいないとシフトレバーをPやNから動かせないなど、意図しない変速を防いでいます。
「誤操作を物理的にできなくする」ことで、そもそも危険な操作が行われる可能性を低くするわけです。ただし、フールプルーフをやりすぎると逆に使いづらくなるケースもあるので、操作性とのバランスも考える必要があります。
「リスクアセスメント」の流れに安全設計組み込む
安全設計の手法はわかったけど、「どのように取り組めばいいの?」という疑問を持つ方も多いと思います。鍵になるのがリスクアセスメント。リスクを評価して対策を考えるリスクアセスメントのプロセスの中で、安全設計の手法を実行しましょう。
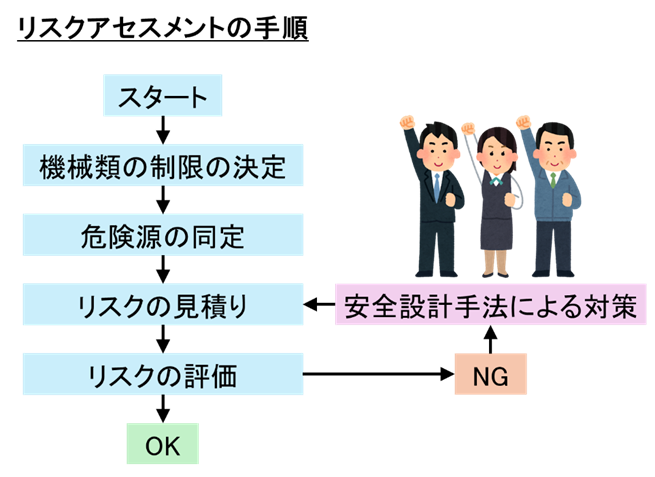
リスクアセスメントの基本的なステップは上図のようになります。
機械類の制限の決定
設計対象となる機械の用途や使用範囲、さらには稼働環境(温度・湿度・設置場所など)を明確にします。たとえば「どのような作業を想定している機械なのか」「使用者はどんなスキルレベルか」「室内で使うのか屋外で使うのか」などを細かく決めることで、今後の危険源の特定やリスク見積もりがより正確になります。
危険源の同定
機械の構造や動作、使用環境をチェックし、「どんな危険があり得るか」をリストアップします。
具体的には、回転部分への巻き込みや、刃物・切削部との接触、落下・転倒といった物理的な危険源だけでなく、電気的・熱的・化学的な要因も含めて洗い出します。例としては、工作機械なら回転軸や切断機の刃、搬送装置なら落下や衝突など、考えられるあらゆるシナリオを想定しておくことが大切です。
リスクの見積
危険源をリストアップしたら、それぞれのリスクを「どのくらいの頻度で起きそうか」「もし起きたらどの程度の怪我や損害になるか」という観点で見積もります。
ここでは、リスクを「危害のひどさ×発生確率」で評価することで、優先的に対策すべきリスクを洗い出します。
リスクの評価
見積もったリスクを基準(社内規格や国際規格など)と照らし合わせ、「許容できるか・できないか」を判断します。許容できないレベルのリスクについては、フェールセーフやフォールトトレランス、フールプルーフといった安全設計手法を駆使して対策を講じます。
対策後に再度リスクを見直し(残留リスクの確認)、最終的に「十分に低減された」と判断できる段階まで繰り返し評価を行いましょう。
最後に
機械設計では「リスクをゼロにする」よりも「可能な限り小さく抑える」ことが現実的です。
筆者もこれまで、フェールセーフ・フォールトトレランス・フールプルーフなどの手法を駆使しながら、コストや納期とのバランスで悩む場面に何度も直面してきました。それでも、リスクアセスメントを行い、各安全設計手法を上手に組み合わせることで、大きな事故やトラブルを回避できています。
初心者の方には、「許容できないリスク」を早い段階で把握し、それをどう抑え込むかを考えるクセを身につけてほしいと思います。
経験を積むほど、「ここはフェールセーフで安全側に倒す」「ここはフールプルーフでミスそのものを起こさせない」など、経験的に判断できるようになります。安全設計を意識した機械はユーザーからの信頼も高まるので、ぜひ今回紹介した考え方を、あなたの設計現場でも役立ててみてください。