インダストリー4.0の一般的な定義はこちらになります。
「インダストリー4.0」とは「第4次産業革命」という意味合いを持つ名称であり、水力・蒸気機関を活用した機械製造設備が導入された第1次産業革命、石油と電力を活用した大量生産が始まった第2次産業革命、IT技術を活用し出した第3次産業革命に続く歴史的な変化として位置付けられている。
インダストリー4.0の主眼は、スマート工場を中心としたエコシステムの構築である。人間、機械、その他の企業資源が互いに通信することで、各製品がいつ製造されたか、そしてどこに納品されるべきかといった情報を共有し、製造プロセスをより円滑なものにすること、さらに既存のバリューチェーンの変革や新たなビジネスモデルの構築をもたらすことを目的としている。
総務省
インダストリー4.0は製造業における大きな変革であり、ドイツ政府が2011年に発表しました。
大きく分けると2つの段階に分解できます。
- 第1段階「情報を共有し、製造プロセスをより円滑なものにする」
- これは主にIoTとデジタルツインを軸とした生産システムの効率化を指しています。
- 第2段階「既存のバリューチェーンの変革や新たなビジネスモデルの構築」
- これについては様々なアイデアが求められますが基本戦略としては、ノウハウをサービスとして提供すること考えます。
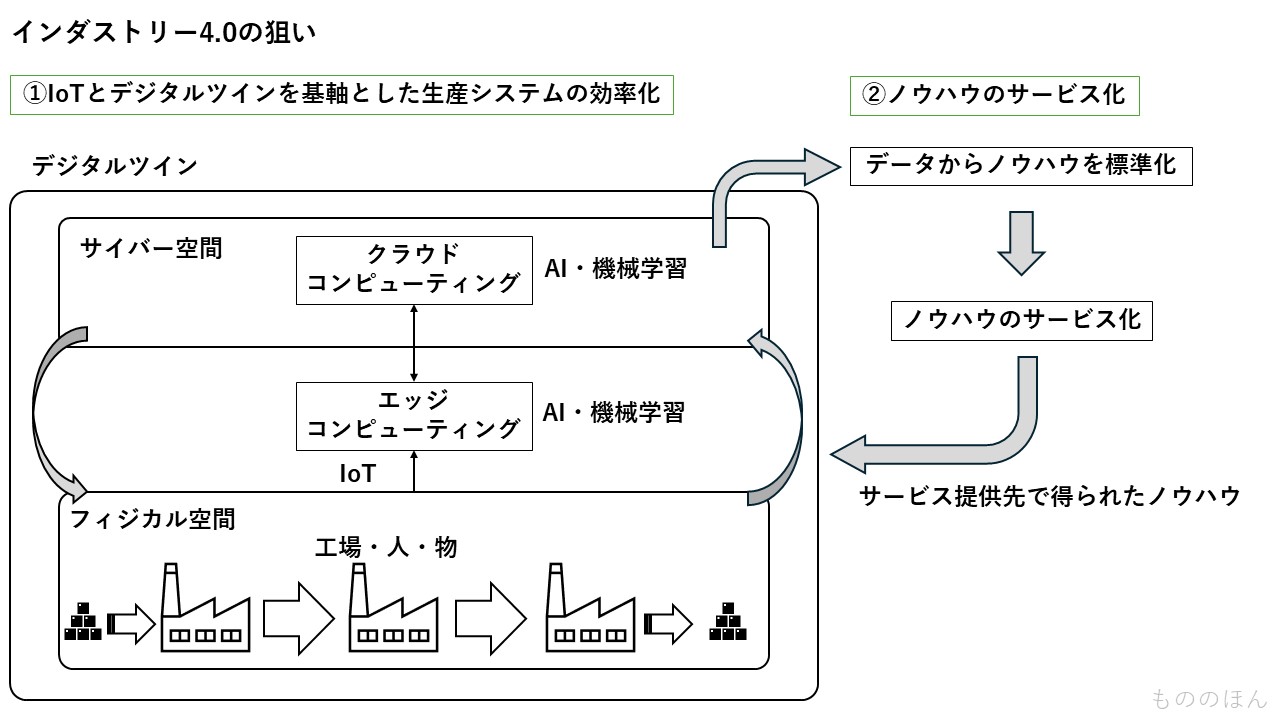
本記事では、まず現代の生産システム(TPS)について触れた後、①IoTとデジタルツインを軸とした生産システムの効率化をどのように行うか解説します。その後、②ノウハウをサービスとしてどのように提供するかについて解説します。
単なるデジタル化推進ととらえてセンサーの追加と予知保全ばかりに目が行っているようでは勿体無いことをご理解していただけたらと思います。
インダストリー4.0で実現する「生産システムのバージョンアップ」「ノウハウのサービス化」
インダストリー4.0とは、製造業においてIT技術を取り入れ改革を図ります。改革によって「生産システムのバージョンアップ」と「ノウハウのサービス化」の2つの実現を目指します。
インダストリー4.0は生産システムをバージョンアップさせる
インダストリー4.0の目的のひとつは、既存の生産システムの更なる効率化です。
ここで既存の生産システムとは、トヨタ自動車が開発したTPS(ToyotaProductionSystem)のことをさしています。
生産システムにはいろいろな方式(ライン生産、ロット生産、オーダー生産、リーン生産等)がありますが、現代の多品種少量生産に適したTPSをベースに生産の効率化を図って行きます。
TPSとは無駄の削減
TPSの特徴を抑えましょう。TPSは無駄を最小限にするために開発されました。(無駄とは在庫を指します)
TPS以前は見込生産であったため、必要数をまとめて作って次の工程、またそこでまとめて作って次の工程というような体制でした。
例えばAという製品を作るために部品B,Cが1つずつ必要だとします、BとCを作るのにそれぞれ10分と20分かかるとすると1時間でBは6コ、Cは3コ完成します。
できた部品をAを組み立てる工程に持っていき、Aを3コ完成させるとBの部品が3コ在庫として残ります。
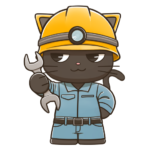
この在庫が無駄になります。実際に製品を作るには何百もの部品があり、企業をまたいだ何十もの工程があるためどんどん在庫が積みあがってしまいます。
要するに、見込生産では前工程から計画して計算するので、それが後ろの工程で大きな差になって来ることが問題でした。
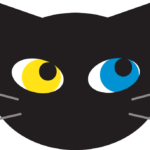
在庫は多くの無駄を生み出します。まず保管場所、保管場所の土地代、移動させる時間、移動させる人、移動させる機械、数が多くなってくると管理システムも必要になります。さらに、長期在庫品には経年劣化のリスクも出てきます。
とにかく在庫という無駄を最小限にしたい!という思いのもとに開発されたのがTPSです。
TPSのポイントは次の2つです。
ジャストインタイムとカンバン
前工程から計画するために在庫が積みあがってしまうので、TPSでは、後工程から生産を計画します
つまり、後工程で必要な数を必要なタイミングで入手できるようにしました。これをジャストインタイムと呼んでいます。ジャストインタイムを実現するツールとしてカンバン方式が採用されています。
具体的には、後工程で部品が足りなくなってきたらカンバンに「部品Bを5コ」と書き、前工程に送ります、前工程はカンバンが届いたら部品Bを5コ後工程へ送り、不足した5コを作る準備に移ります。これにより後工程で必要以上の在庫を抱えることがなくなりました。
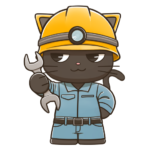
ジャストインタイムはTPSのコンセプト、カンバンはルールといえます。
そして、次の二つはルールを守るために編み出した工夫の結晶です。
平準化と多能工化
平準化とは、小ロットで生産を行うことです。平準化のいいところは、人や工場などの設備投資が小さくて済む点です。
ジャストインタイムとカンバンにより前工程は後工程の依頼に応じて生産を行います、この時に後工程のロットが大きいと前工程もそれに対応した設備を持つ必要が出てきます。
後工程は比較的大きな企業が担っていますが、前工程になるほど企業規模が小さくなるので生産に耐えられる設備を投資できない等の問題が生じます。このため、ジャストインタイムとカンバンをサプライチェーン全体で行うためには平準化した生産システムが必要になっています。(設備投資が小さくて済むのでコロナ時のような急な景況の変化にも対応しやすくなります)
平準化した生産システムでは多様な製品を作るため、製品ごとに段取り替えが必要になったり、製品ごとに異なる作業を行ったりするようになります。このように一人の作業者が生産に合わせて多種多様な作業を行うことを多能工化と呼びます。
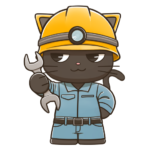
段取り替えの高速化を実現し多様な設備を使いこなし多能工化するためには人間の努力と工夫が必要です。
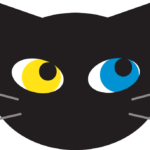
平準化を行い、多能工化を極めることは、多品種少量生産や景況に強靭になるんだね。
無駄の最小化とサプライチェーン全体での効率化
インダストリー4.0はTPSが実現した無駄の削減をさらに進化させます。
リアルタイム化による無駄の最小化
IoTにより物の移動や人の動きなどの正確な情報がリアルタイムで収集できるようになりました。かつては数時間単位の周期で動いていたカンバンがリアルタイムで稼働するようになり、AGVなどの機械で連続的に搬送できるようになったことにより最小在庫数の更なる削減が実現されました。
リアルタイム化によるサプライチェーン全体での効率化
収集したデータはリアルタイムで生産スケジューラやMES等を使って構築したデジタル空間に反映され統合管理されます(デジタルツイン)。さらに、AIや機械学習を用いてサプライチェーン全体での最適化を図れるようになったためこれまで難しかった工場間や企業間での情報伝達のラグを吸収するための在庫も最小化が可能になりました。
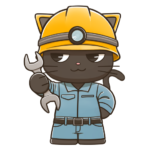
インダストリー4.0によってこれまで以上に時間と距離の壁が破壊され、さらに、正確な情報を基にした即時判断が効率化を進めたんですね。でもこれだけだと単なる効率アップです。インダストリー4.0の狙いを正しく理解するにはここからが重要です。
インダストリー4.0はノウハウをサービスにできる
インダストリー4.0のもうひとつの狙いは、ノウハウのサービス化です。(製造業のサービス化とも言われます)
サービスとして提供するには自分たちが持っている何に価値があるのかを分析する必要があります。また、熟練者のみが分かる暗黙知のままでは顧客にノウハウを伝えることができません。
そのため誰もが分かり活用できる形式知へと標準化することが最初のステップになります。
その後、自分たちが持っているノウハウにあわせてサービス化をどのように展開するかのステップに進みます。
ここでは、「標準化」と「サービス化」の2つのステップに分けて解説します。
デジタル技術でノウハウを標準化する
標準化とは「業務について、関係者が合意して手順や成果物の水準などを決定し、誰もが業務をできるようにすること」を指します。
インダストリー4.0は後で解説する「基本ツール群」を中心にしたデジタル技術を用いて標準化を進めます。
製品設計やライン設計の3D化やIoT活用による機器管理などはインダストリー4.0以前からデジタル化が進んでいました。例えば、機器の動きに関しては、センサーを通じて得られた稼働状況の数値データをモニタリングすることで管理や分析が可能となっています。
しかし、熟練技能者をはじめとする人の作業のデジタル化や数値化は難しく進んでいませんでした。人の動きや作業を分析するためには、複数のセンサーを組み合わせなければならず、大量のデータの分析を行うことが不可能だったためです。
その上「どのような作業であればより生産性が高く、品質が良いのか」といった基準や閾値の設定も非常に困難なため現場や熟練技能者の動きはデジタル化しづらい領域でした。
しかし、インダストリー4.0以降はコンピュータの進化により大量データの処理が可能になったり、AIや機械学習により「どのような作業であればより生産性が高く、品質が良いのか」の因果関係を分析できるようになったりしたことで多くの領域のデジタル化が可能になりました。
ノウハウをサービスとして展開する5のパターン
次は標準化したノウハウをサービスとして展開する方法について解説します。次の表で示すように「どんなノウハウを提供するか」の観点で5つのパターンに分けられます。
サービスとして展開する5のパターン
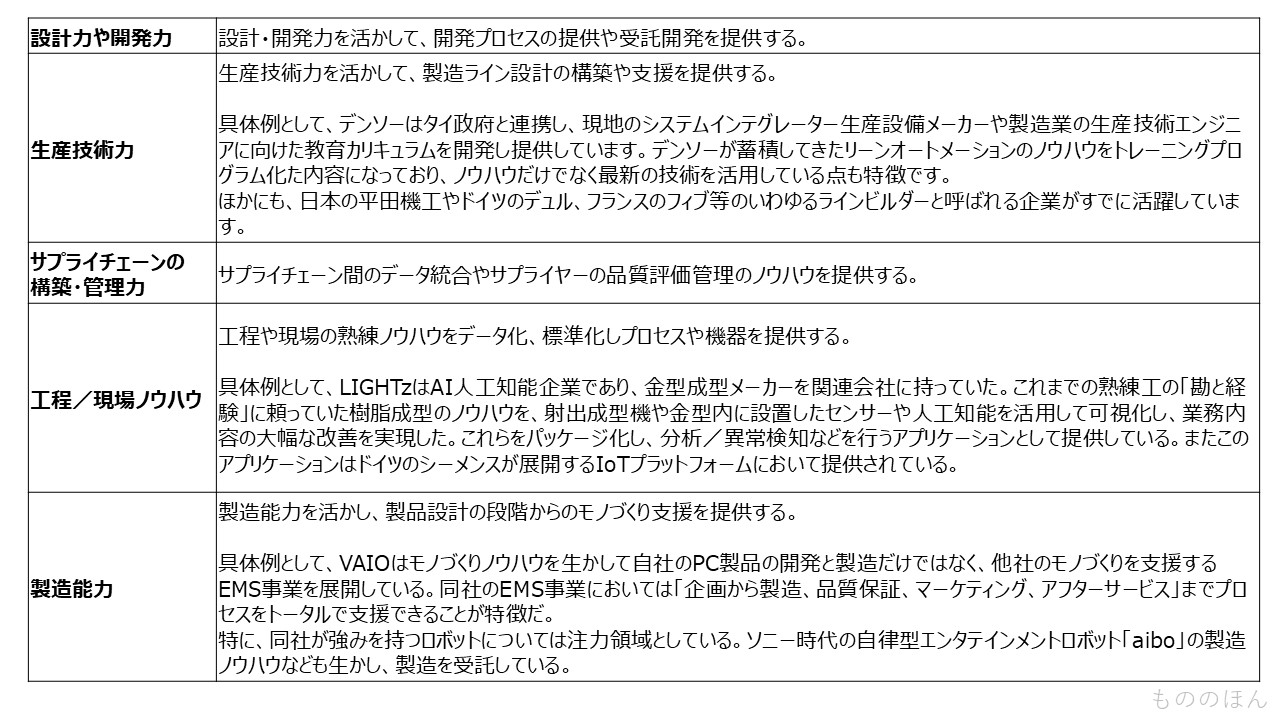
オープンにする範囲とクローズにする範囲を見極めて勝つ
ノウハウのサービス化についての重要な留意点として、「自社のコア技術を他社に提供すると、自社の競争力は失われてしまう」という点について補足します。
当然ながら、コア技術を他社に提供してしまうと自社の競争力は失われてしまいます。しかし、自社の業務内容や技術内容を分析すると、全てがコア技術ではないことが分かります。重要なことは 「コア技術領域と非コア技術領域の区別」です。
コア技術についてはサービスとして提供するしないにかかわらずクローズ(機密)状態を確保する必要があります。そして、非コア技術についてはオープンにしてサービスとして提供たり、自社で保有することをやめラインビルダー等に外注することでコア技術に専念したりします。
つまり、自分たちがどの領域で勝ち(価値)を狙うかの見極めが大切です。
インダストリー4.0の「基本ツール群」を理解する
ここまでに解説した「生産システムのバージョンアップ」「ノウハウの標準化」「ノウハウのサービス化」を実現するために様々な技術や手法が確立されてきています。
インダストリー4.0の「基本ツール群」9選
インダストリー4.0で活用されている様々な技術や手法の中から重要な9つをピックアップして解説します。
「基本ツール群」9選
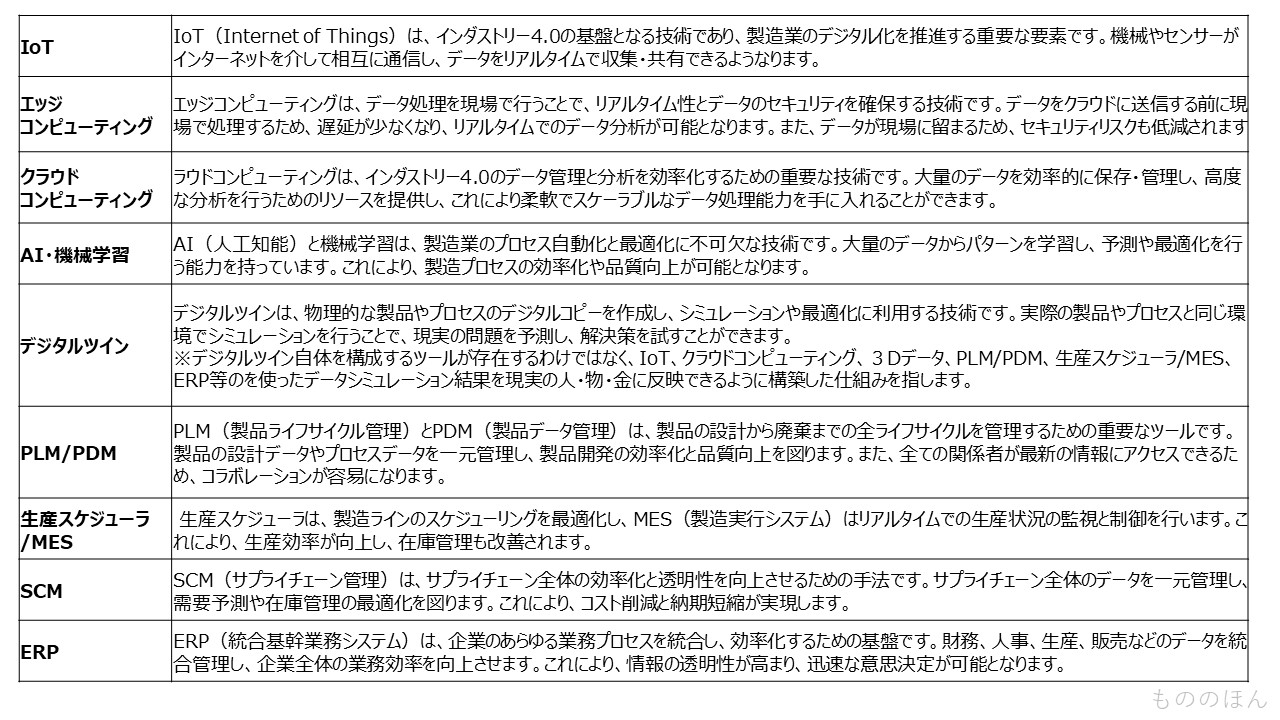
インダストリー4.0の設計原則
「基本ツール群」は次の設計原則に基づいて設計されています。大事な思想ですので掲載します。
インダストリー4.0の設計原則
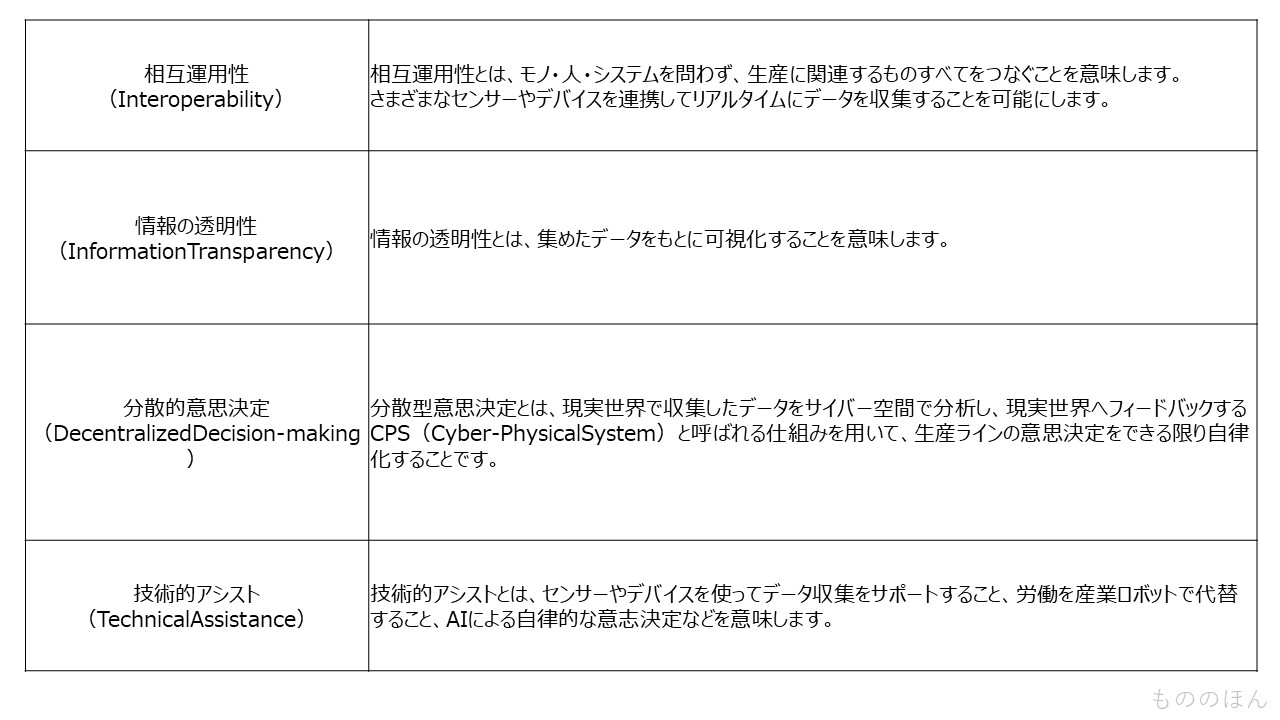
終わりに(世界から見て遅れている日本のポテンシャル)
日本の製造業はGDPの20%程度を支える基幹産業でありかつては世界一のモノづくり大国でした。しかし、デジタル化の遅れやかつては強みであった属人的ノウハウに依存するが故のグローバル化への遅れにより存在感を失いつつあります。
さらに、インダストリー4.0により加速した水平分業化(かつては自社でそろえなければいけなかったノウハウが既にサービスとして売られているので買ってくれば良い)により80%のモノづくりは調達できるようになったともいわれています。
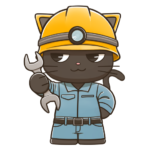
つまり、アイデアさえあれば80%のクオリティの製品であれば誰でも作れるようになってきています。
このような状況の中で日本のモノづくりは今後どのように勝っていけばいいのか。
筆者は、80%のモノづくりの提供者になることと同時に、調達できない残りの20%をどう構築するかが競争力を保つための重要なポイントになると思います。
日本の製造業は個々の顧客に「深く」寄り添い、それぞれにカスタマイズした事業開発を強みにしてきました。これら個別の工程や現場の技術、ノウハウを丁寧にデジタル化していくことで、競争力のあるサービスが生まれると信じています。
本記事では、インダストリー4.0についてできるだけ簡単な解説を目指しましたが、かなり長い記事になってしまいました。ご精読ありがとうございました。
本ブログでは、製造業にかかわる重要キーワードについて解説しています。よろしければ他の記事もご覧ください。あなた様のレベルアップにつながれば幸いです。
また、本ブログではモノづくりの学習のために技術系最高峰の資格「技術士」の取得をお勧めしています。よろしければこちらの記事もチェックしてみてください。
参考資料
本記事は、次の情報を参考に作成しております。ご興味ある方はぜひご覧ください。